If your company is a large user of electricity (generally over 100 MWh/yr), it is likely that you are paying a fairly hefty charge for peak demand. It can be as much as 50% or more of your bill!!
So, what is peak demand and how can you manage it?
Every time a light or a piece of equipment is switched on it creates a ‘demand’ for electricity. There is also (understandably) a customer expectation that this demand will be met 24/7 and 365 days a year. But this ‘guaranteed’ supply comes at a cost!
Electricity infrastructure such as generator stations, high voltage transmission lines and distribution wires are constructed to meet the energy demands of an area. If the demand is greater than the supply, electricity providers may need to invest to upgrade infrastructure to meet customer requirements. Distributors obviously need to recoup such investment and the ongoing maintenance cost of a larger network.
Interestingly, in South East Queensland, 16% of the network has been built to service a peak demand that only occurs for a few hours on a few days of the year! ( Energy Queensland Group, 2017, Energex Peak Demand, www.energex.com.au )
Reducing overall peak demand means less investment in infrastructure and (in theory!) an overall cost reduction for you. As a result, peak demand charges are used by electricity retailers as an incentive to reduce peak usage and the need for more infrastructure.
Normal body text to be “paragraph”.
How are demand charges calculated for my business?
Peak demand is the maximum quantity of electricity your business needs at any point in time. It can be likened to your car’s speedometer that tells you the speed you are travelling at (maximum speed is of interest) and is charged in $/kW or $/kVA. Your overall electricity usage is like your odometer, telling you how far you’ve driven and is charged in $/kWh. The meters measure your demand in 15 minute intervals in a set period (usually a month). You are charged for the set period based on the highest peak you reached even if it only occurs for 15 minutes during that month. The theory is that even though you only draw that quantity of energy from the network for 15 minutes within a month, the distributors must always have the capacity and maintain the infrastructure to cater for that demand.
So, what can my business do to reduce demand charges?
First work out when the peaks in demand occur. To do this you can usually request your usage data from your service provider. Most providers have online systems which you can log into and get up to date data on your usage. If they can’t provide this, they will most likely send you a data file showing your energy use in 15 minute intervals. Graph this data and work out when the peak occurred. You may have a pretty obvious spike (Image 1) or you may have more bumpy terrain (image 2).
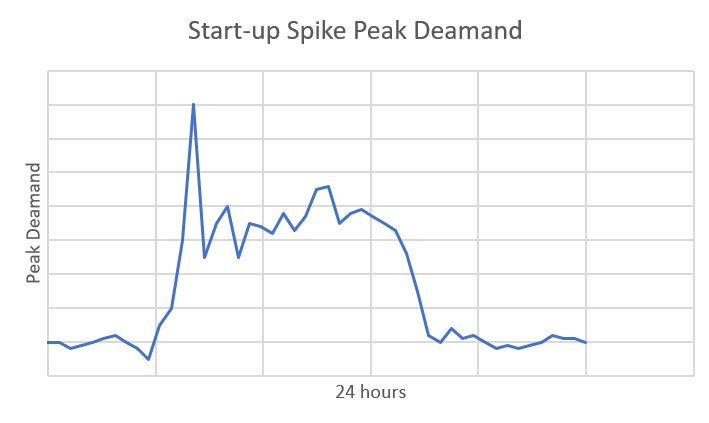
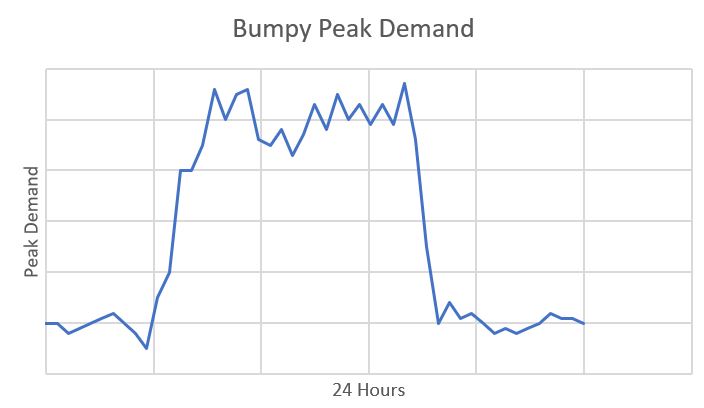
Secondly work out what is causing the peak. This might be quite obvious. Equipment often causes a large spike of electricity demand at start up before reaching a steady state (Image 1). Often this occurs at the start of business each day or after lunch breaks. An electric motor starting-up for example can draw up to five times or more the current that it draws during normal operation. Obviously, spikes can also occur during peak periods of business activity or production or when a particularly energy intensive piece of equipment is turned on (Image 2). Spikes may even be caused by external factors such as hot weather and the demand on air conditioning or cooling units.
Sometimes it can be difficult to peg spikes down to one piece of equipment or one practice. It may just be the ongoing and fluctuating use of equipment over the day, in which case the solution may involve multiple actions.
Take action to reduce the peak. An assessment of opportunities and implementation of energy efficiency measures can help to reduce peak demand charges.
Some more specific examples are given below.
- Start up peak demand can be reduced by staggering the start time of equipment and thus spreading the spike caused by each item of equipment. You may just need to wait 15 minutes between turning on each piece of equipment to allow the first piece to reach steady state. Better yet, don’t turn it on at all until it is needed. One site found that when they turned on the lights to their large warehouse it caused a very large spike with the rest of the day usage being relatively low. Their solution was to break the lights up into smaller banks and only switch on those they needed. They also looked at replacing the lights with LEDs to further reduce their usage.
- If possible, look at re-scheduling equipment start times. If you know that two different operations, product runs or equipment both draw a large amount of electricity then consider if it is possible to schedule them to operate at different times. For example, some foundries with induction furnaces will try to reduce the operation of other equipment while the furnace is running to reduce the peak. Staggering the start times of staff may also assist to distribute the load. Another manufacturing business scheduled their work to have several large jobs in close succession so that they would only have a higher demand for that single month rather than several consecutive months. They also informed their customers of the increased energy costs and the need for a longer lead in time to improve their scheduling. Working with their customers allowed them to keep their costs and prices down.
- Take advantage of the benefits of an Energy Management System. These can be used to automatically alarm when reaching a pre-determined peak level and even ramp non-essential equipment down to minimise the peak. For more information, see our EMS blog.
- Consider if solar power can be used to shave the top off the peak if it occurs during sunlight hours. Similarly, battery storage (charged overnight) could be used to kick in when the peak is being reached.
- Consider changing the way the motors start. A ‘soft start’ draws less power during start up to reduce peak demand. It also reduces damage to equipment by having a lower starting torque. If a high starting torque is required this option may not be appropriate.
- If there is no outstanding contribution to the peak and your energy use is generally steady, think about what other energy efficiency measures you can implement to reduce overall energy use e.g. upgrading to a variable speed motor or changing lighting to LED. An energy audit can be undertaken to determine what opportunities are available to improve your efficiency.
For more advice and help in reducing your peak demand charges contact The Ecoefficiency Group.